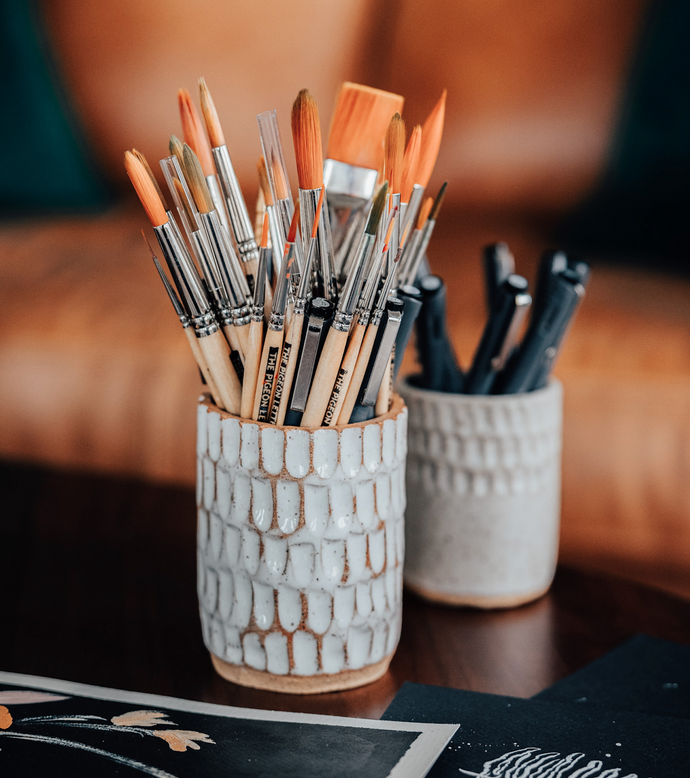
Elevate your creativity with handcrafted ceramics
Ceramics by Peggy Dean
Each piece embraces imperfections, and each wobble, asymmetry, indent, and other handmade quality is intentionally preserved to bring hand built energy into the creative space.
Seeing earth formed by hand reminds me to celebrate my handmade process of creating art while I'm using a functional piece of art. I hope it helps to remind you to embrace your process in its entirety as well because your creative journey is so very special.
No two pieces are alike. ♥
Artisanal Ceramics by Peggy Dean
Explore an exquisite collection of handmade ceramics, crafted with love for artists by an artist. Each piece is one-of-a-kind, adding a touch of uniqueness to your creative process. Find the perfect ceramic companion for your artistic endeavors.
Available pieces
Thanks for letting me share a little piece of my passion with you
🜃 the process
Each ceramic piece created is meant to embrace imperfections, and each wobble, asymmetry, indent, and other handmade quality is intentionally preserved. Seeing earth formed by hand grounds me (no pun intended) and reminds me to celebrate my handmade process of creating art while I'm using a functional piece of art. I hope it helps to remind you to embrace your process in its entirety as well because your creative journey is so very special.
Form
Raw, wet clay is molded by hand and left to breathe for several hours until it reaches a stiff, yet moldable form. It is hand built form the shape of each piece. Pieces may be scored and connected together, pinched and pulled.. and once again left to breathe until it's no longer moldable but still soft enough to carve, if desired. Using a combination of fine steel tools and found nature items, finishing touches are added and often carved at varying lengths and placements for added interest.
Fire #1
After about 40 hours, a piece is fully dry and ready for the first round of firing. It's carefully positioned in the kiln and high fired at 2200F (1204C) for 8 hours, then left in the kiln to cool for another 12 hours. This creates the bisque material from the raw clay and is the perfect preparation for adding glazes.
Glaze
After a piece's first firing, its finished design is determined. Most often, pieces needs to be hand painted with a resistant wax in the areas that won't be glazed. Once the wax has been applied, glaze is mixed to a meticulous consistency that will evenly bond with the bisque ceramic material. Pieces are either fully submerged into a container of the glaze, or the glaze is applied by hand with a brush. When applied by hand, three coats of glaze are applied with dry time in between.
Fire #2
After pieces are glazed, they're ready for a second firing. They head into the kiln again and are high fired for another round. After this, pieces are revealed in their finished result for the first time, and every single time, it's a fun surprise to see how they turn out. sand While a piece is "finished" after a final firing, there are finishing touches that are oftentimes missed in ceramics--the most important being a light sanding to the bottom of pieces to soften the gritty texture. If a piece needs grip, small silicone bumpers are adhered to the bottom.